Renovate or Build New:
A Life Cycle Comparison of Two Academic Buildings
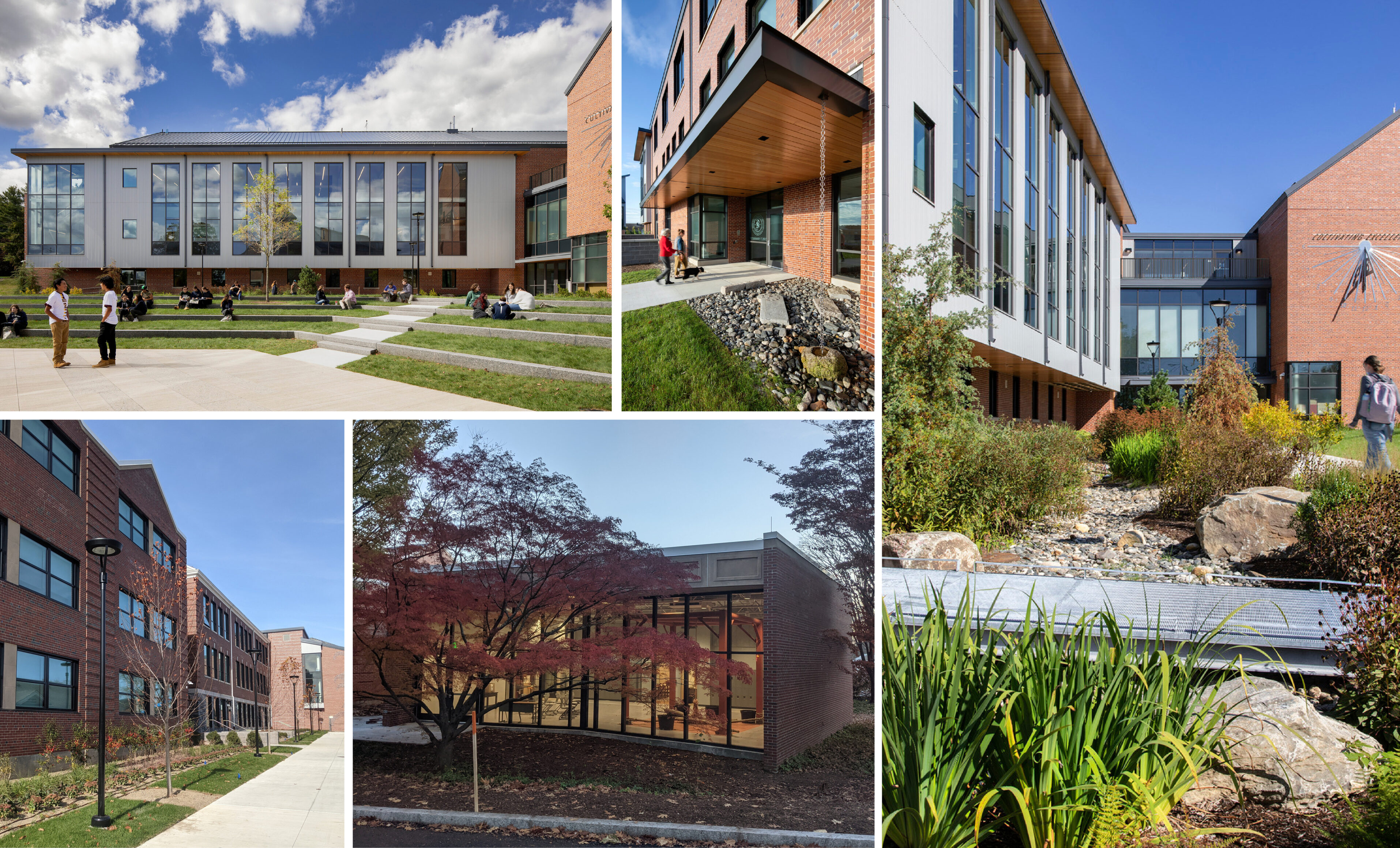
What does a direct comparison between renovation and new construction reveal about a building’s environmental impact and how can this data inform future design decisions?
HMFH sustainability leaders Suni Dillard and Alexandra Christiana addressed these questions with Carrie Havey of The Green Engineer at USGBC Live’s Boston Forum, using a case study of two buildings at Bristol County Agricultural High School to compare the environmental impact of the products associated with renovation vs. new construction.
In recent years, there has been a push in the design industry to reuse existing buildings as a strategy to limit the greenhouse gas emissions that arise from the manufacturing, transporting, installing, maintaining, and disposing of building materials ₁. The idea seems simple: reuse buildings and reduce carbon emissions. However, the answer isn’t always so straightforward. How a building is reused or built new significantly affects its carbon footprint, so it is important to understand the impact of all design decisions in order to create environmentally responsible buildings.
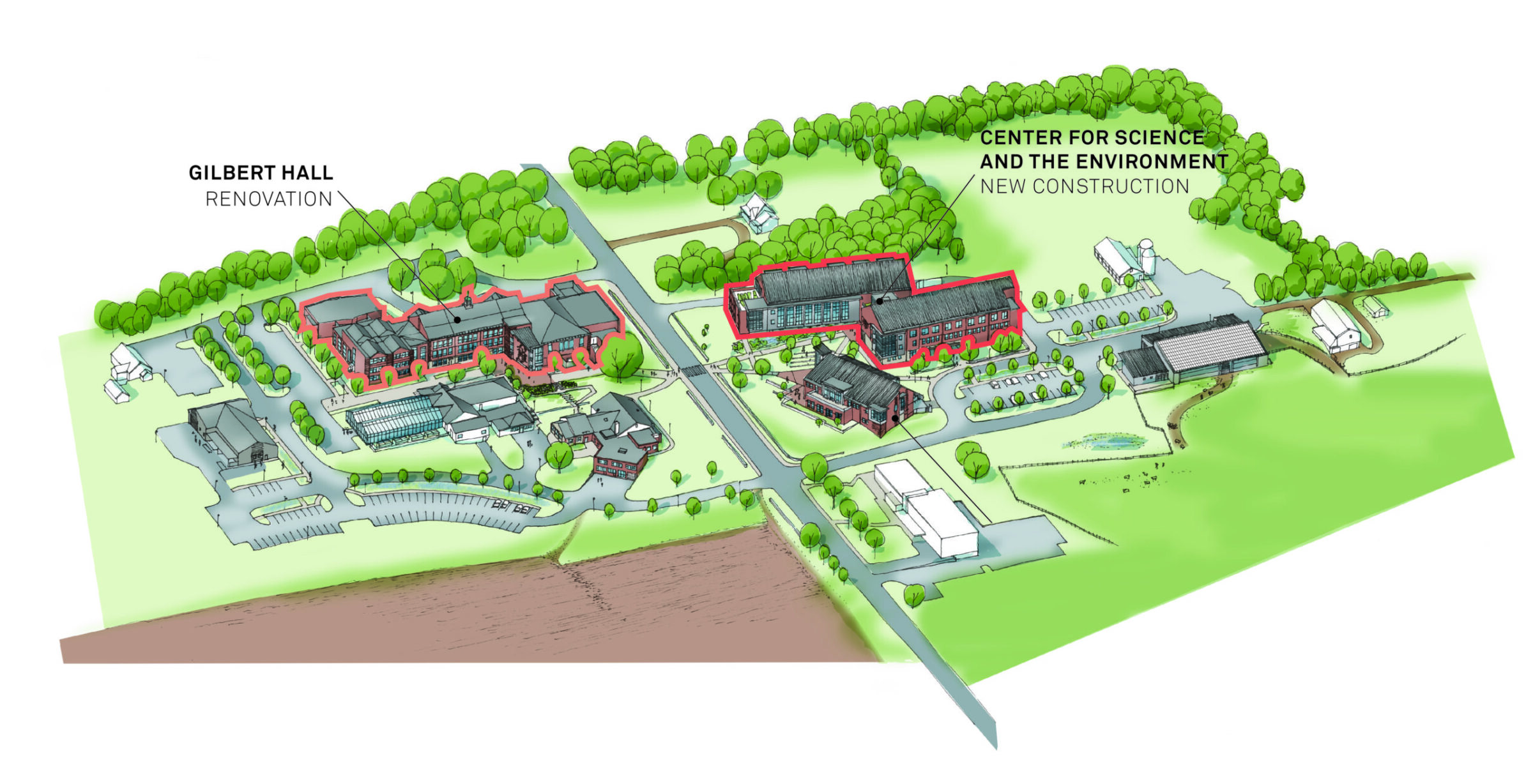
While renewing and expanding the Bristol County Agricultural High School campus, HMFH had the unique opportunity to design two buildings with comparable program and scale. Using Tally, a Revit plugin that quantifies the environmental impact of building materials ₂, we conducted a life cycle assessment analyzing the products specified in both the renovation of Gilbert Hall, a 72,000 SF academic building from 1935, and the new Center for Science and the Environment (CSE), a 73,500 SF academic building, to weigh the benefits of renovations vs. new construction.
A life cycle assessment (LCA) is an analysis of a project’s impact throughout its lifespan, from the gathering and transportation of raw materials, to reuse after a building’s end of life. A completed LCA evaluates factors including global warming potential, acidification, eutrophication, smog formation, ozone depletion, and depletion of nonrenewable energy sources. In North America, there is currently not enough data to include site or mechanical, electrical and plumbing (MEP) systems in a LCA despite their significant impact on a building’s sustainability. Therefore, our analysis of Gilbert Hall and the CSE focuses on the environmental impact of building materials.
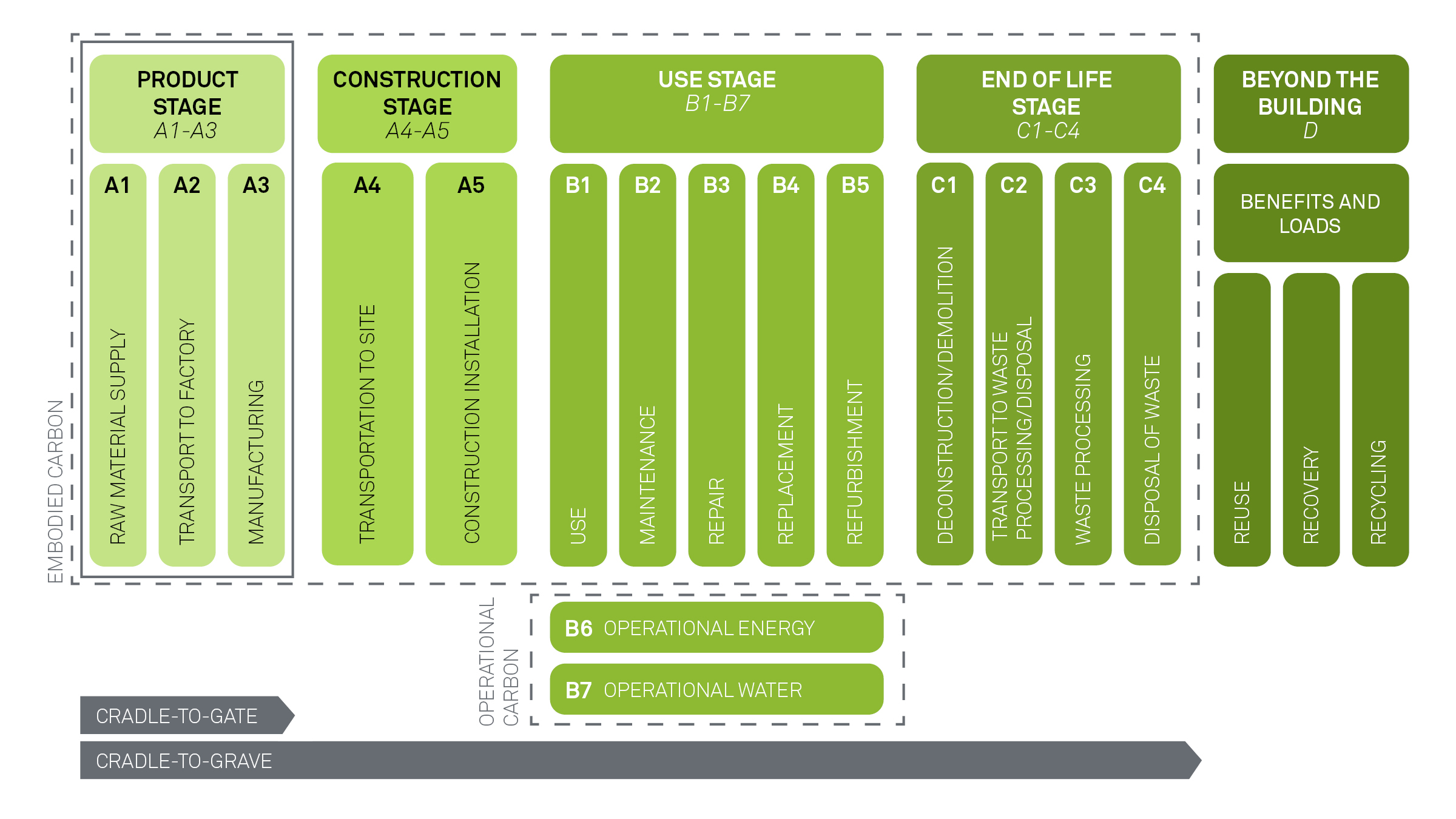
By comparing data from the LCA cradle to gate stages for Gilbert Hall and the CSE, we were able to review the impacts of raw material extraction, manufacturing, and transportation for each project and learn which building elements and product categories are most beneficial in the design of a renovation vs. new construction project. This comparison looks specifically at global warming potential—a relative measure of greenhouse gas contribution over a 60 year-time horizon. For example, the LCA shows the renovation of Gilbert Hall has a 28% reduction in overall global warming potential (calculated in kg C02e) in the cradle to gate stage compared to the newly built CSE.
Building Elements
CSE: 353.3 kg CO2eq/m²
GH: 259.41 kg CO2eq/m²
The newly constructed CSE features a highly efficient exterior wall design, while Gilbert Hall excels in its minimal impact by reusing the existing structural elements.
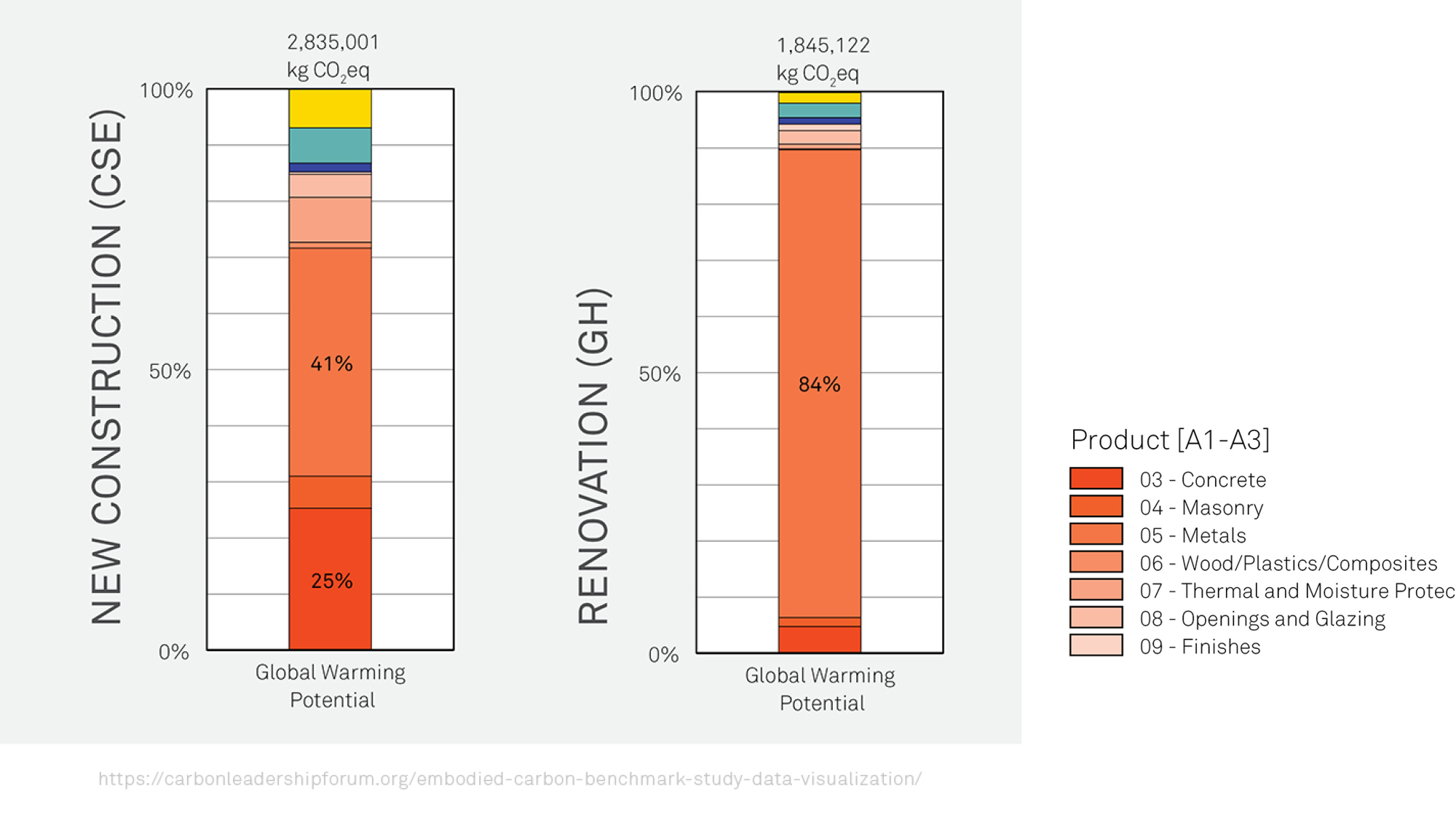
Metals
CSE: 173.31 kgCO2eq/m²
GH: 230.64 kgCO2eq/m²
The lack of concrete used in GH’s renovation resulted in the majority of its material impact being attributed to metals within the enclosure.
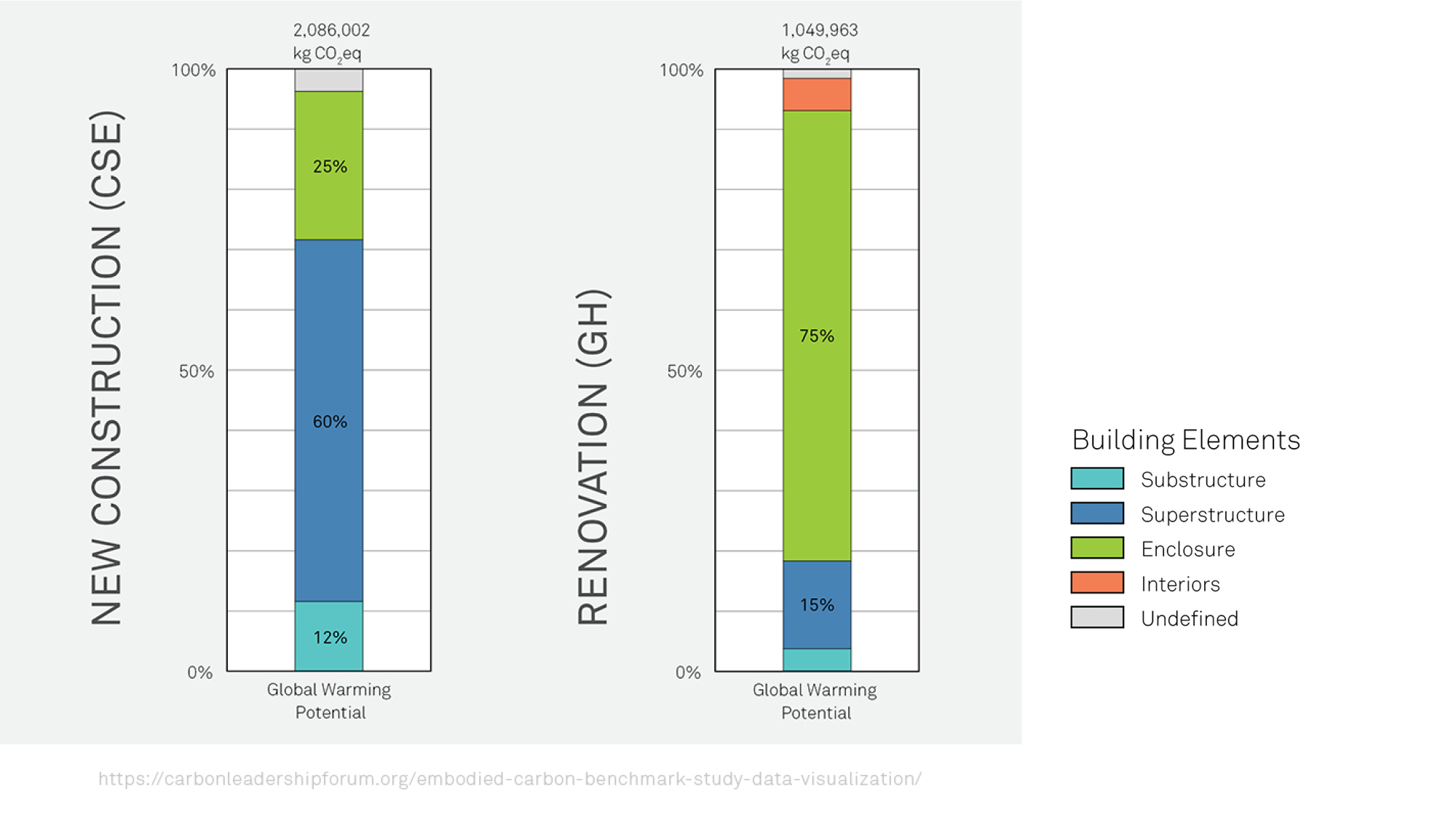
While renovation is often the most sustainable option, a comprehensive understanding of each design element’s impact at all phases of a project promotes the most environmentally responsible choices. Life cycle assessments provide concrete data that can guide clients through a sustainable building process by weighing the impact and effectiveness of each decision over the course of the project. Where do we go from here?
Suggested Workflow
- Pre-Design: Set benchmarks and targets, and demand low carbon materials/transparency
- Schematic Design: Analyze, track and compare embodied carbon against benchmarks and achievable low carbon goals
- Design Development: Prioritize healthy materials, create low carbon specifications, and conduct a carbon estimate
- Construction Documents: Continue to refine low carbon specifications, and require the general contractor to prepare a carbon estimate for construction
Suggested Carbon Reduction Strategies
- Reduce the use of concrete, or substitute fly ash and/or slag for cement in the concrete mix*
- Substitute precast hollow concrete floors for composite metal deck floors
- Substitute cross-laminated timber for metal deck floors
- Utilize glulam columns and beams in lieu of steel columns and beams
*Use of this as a replacement needs more study due to concern over material health issues
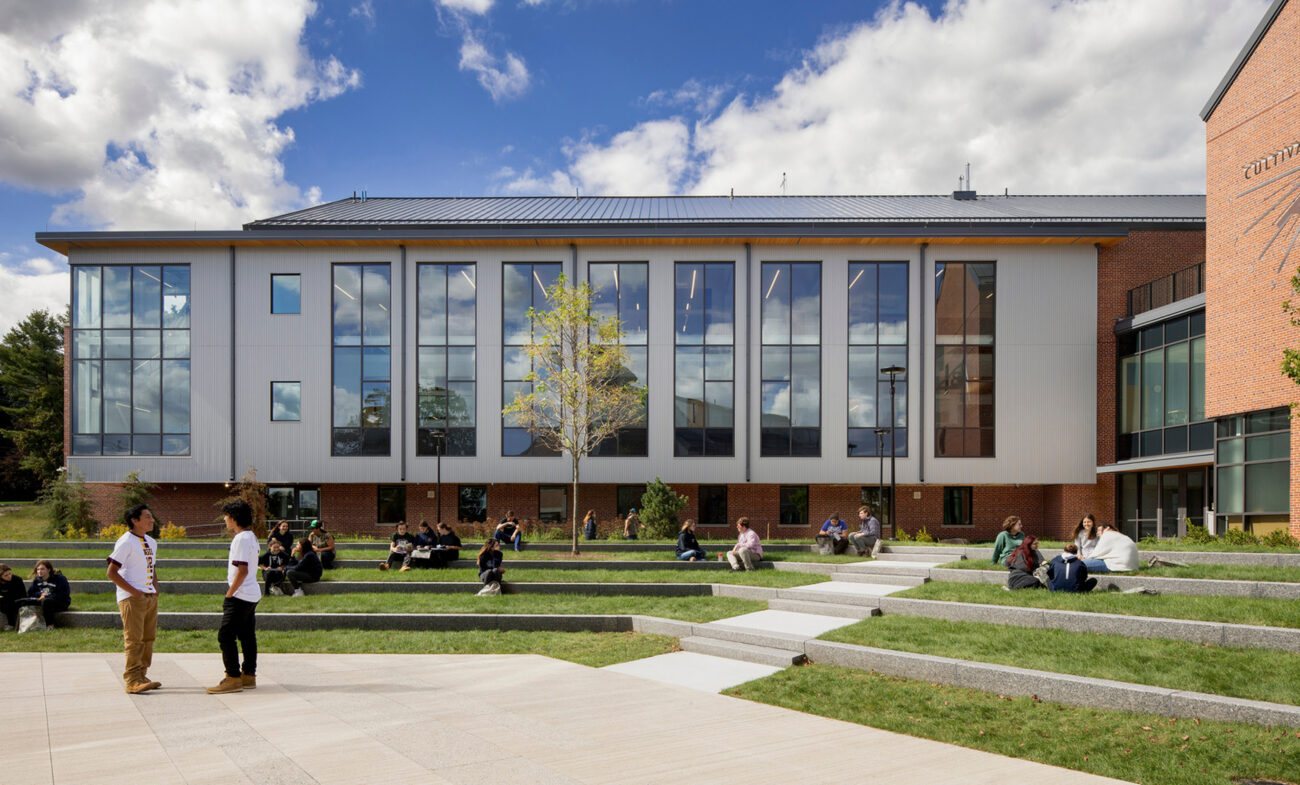
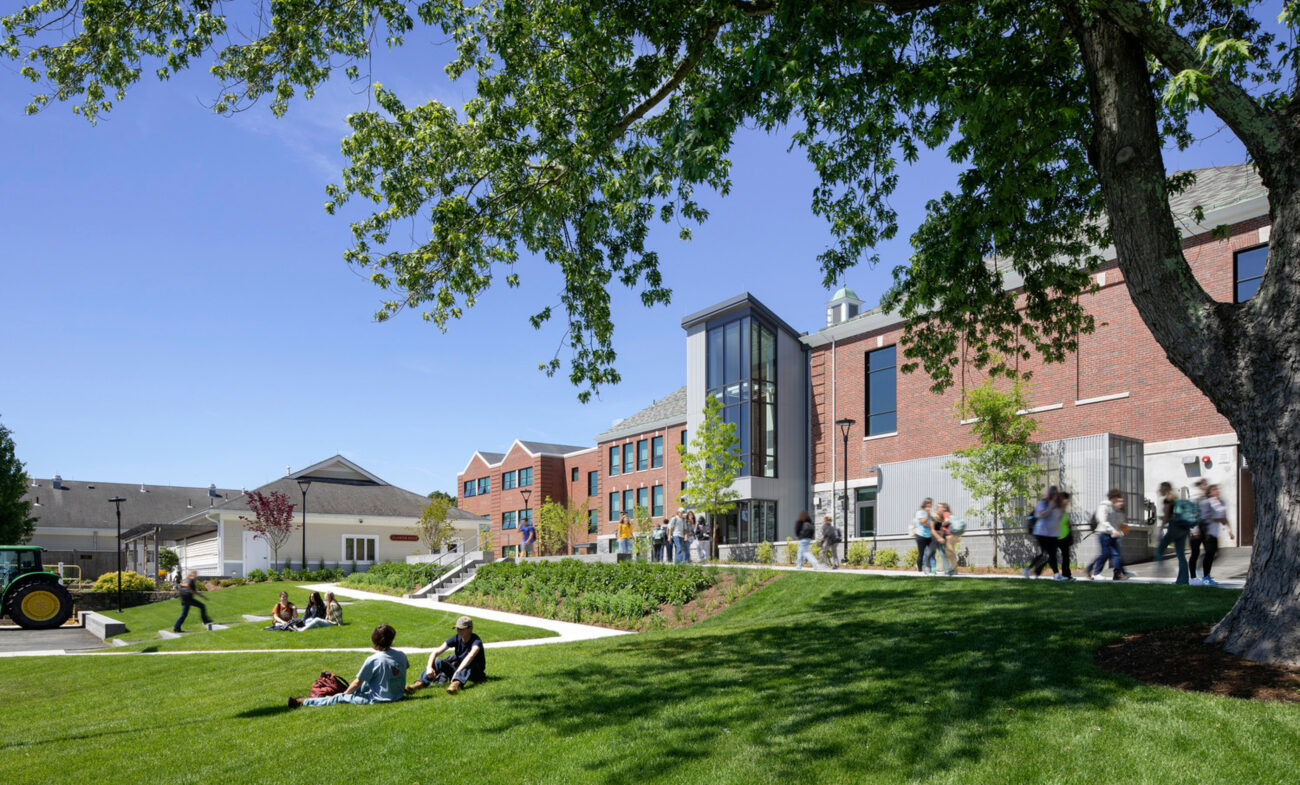